Formulating an enterprise-wide strategy to increase automation is a top but challenging priority for organizations. Increased demand to drive efficiency and reduce costs means that process automation is a priority to support initiatives such as customer experience, operational excellence, and risk. Automation initiatives such as Orchestration, Robotic Process Automation (RPA), Intelligent Document Processing (IDP), and more recently autonomous AI Agents, are helping enterprises to achieve significant cost savings and heighten employee productivity. However, the road to reaping these rewards has proven challenging, with nearly half of organizations stumbling on their automation journey.
To meet the demand for results from "hyperautomation" (the intelligent and integrated use of multiple automation technologies, depending on needs) and to continue to gain budget to support automation efforts, business and technology leaders must focus on projects that deliver predictable value. Here is where process mining fits in the hyperautomation stack. Process mining allows business analysts to derive accurate estimates of automation ROI and to monitor those benefits as they are realized. In many ways, process mining is like an “HR system for automation”, helping us with recruiting, training, performance appraisals, retraining, and potential retiring and rehiring of the right automation technology, whether it's Orchestration, RPA, IDP or AI Agents, when needed.
How can automation decisions be improved with process mining?
According to Gartner, hyperautomation covers a range of automation interventions, all the way from orchestrating entire end-to-end processes via an iBPMS solution, to automating individual tasks via RPA bots, and integrating multiple systems with APIs to glue together different activities in a process. Each automation intervention requires an investment. With limited resources and high ROI expectations, automation leaders are constantly confronted to the question of how to maximize the bang for the automation buck?
Process mining allows automation teams to frame their hyperautomation efforts to deliver consistent business value. First, process mining allows managers to discover their “as is” processes from data comings from their CRM, ERP, and other systems. Second, process mining identifies bottlenecks, rework, and deviations in end-to-end processes, and their root causes, allowing managers to derive deep insights into how to tackle the friction points that are holding down operational efficiency and customer excellence.
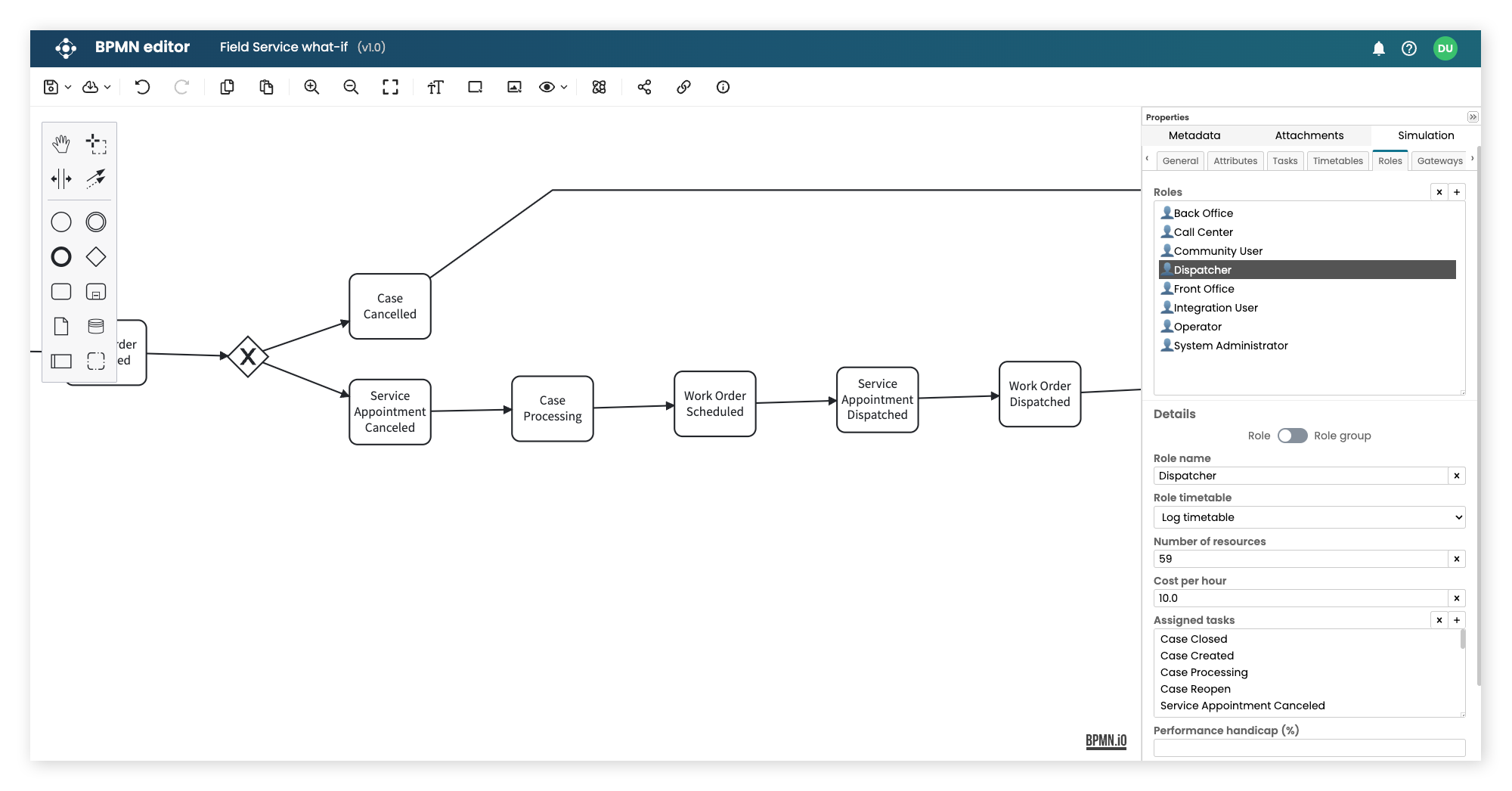
Turn Insights into Interventions
Armed with these insights, managers then identify automation interventions to tackle these friction points. Managers can then test these automation interventions via high fidelity simulation models discovered from the data. These simulation models act as digital twins of the process, enabling managers to estimate how much will they save if they invest into an automation effort, or by how much they would reduce SLA violations and defects in the process.
Digital Process Twins: Bridging Between Business and IT
Apromore’s digital process twin capability goes one step further by enabling managers and analysts to automatically compare the “as is” process, before automation, against multiple “what-if” automation scenarios, and to generate a Process Automation Assessment Report (PAAR).
This report provides a detailed quantification of the benefits that one or more automation opportunities can bring in terms of process durations, costs, and resource utilization metrics among others. And if the organization is using MuleSoft RPA, the business stakeholder can automatically submit the data in this report to MuleSoft RPA Manager’s digital backlog, so that IT teams can pick them up for implementation.
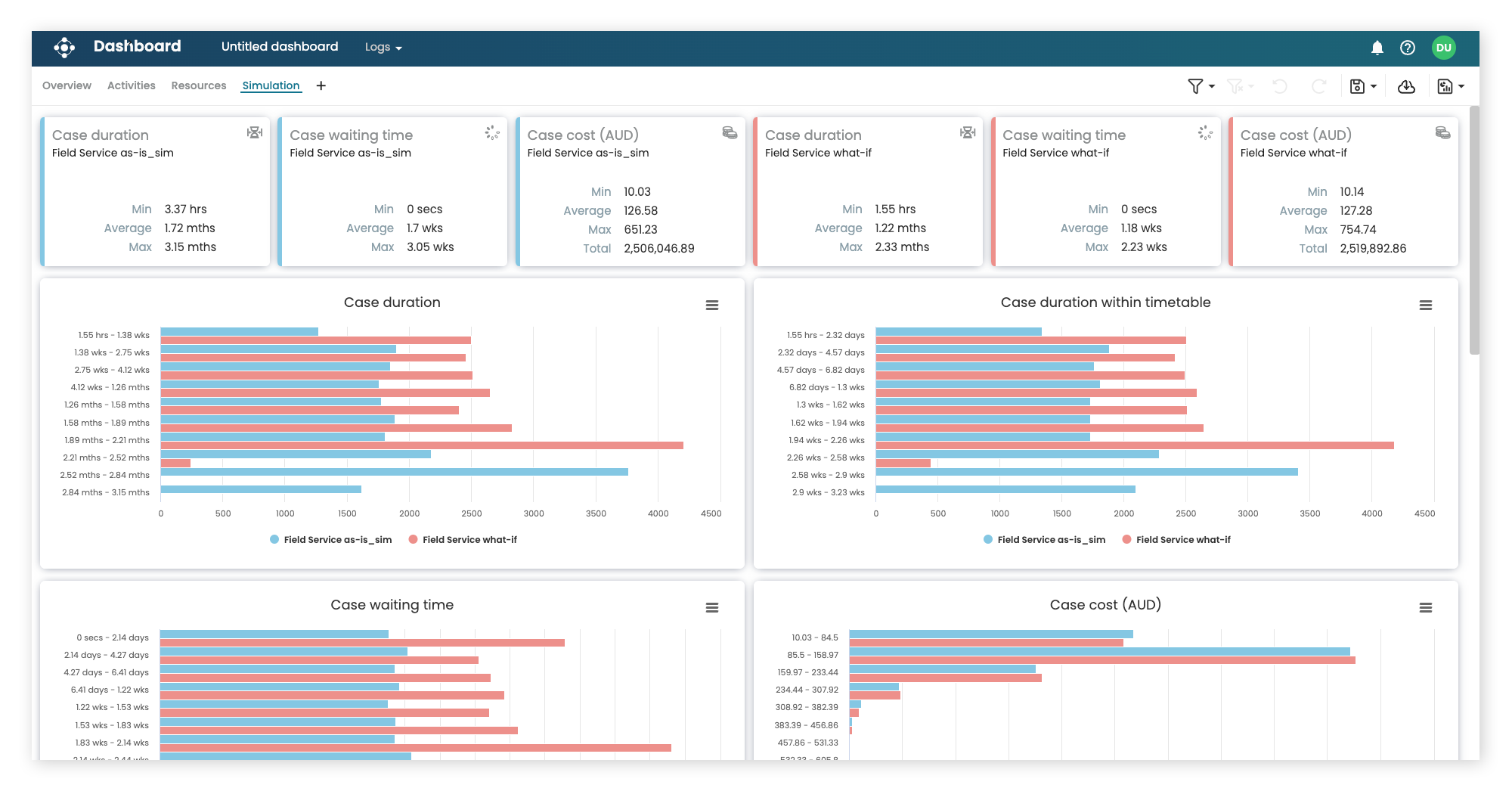
Crucially, all this happens in a fully no-code manner. Starting from data about an end-to-end process, business stakeholders discover the process, generate the digital process twin, simulate one or more automation scenarios, and generate a PAAR, with a handful of clicks, without having to involve data scientists or IT teams. This no-code approach is essential to achieve fast time to value.
Once an automation opportunity has been implemented, process mining enables managers and operational staff to monitor the performance of the process post-automation via real-time operational dashboards. In this way, managers have a detailed and up-to-date picture of the realized ROI of automation initiatives, backed by data and hard numbers.
This real-time monitoring capability also enables managers and operational stakeholders to detect degradations in the performance of the process caused, for example, by misconfigured RPA bots or API integrations, and to quickly escalate these issues to IT teams to ensure sustainable value realization from hyperautomation efforts.
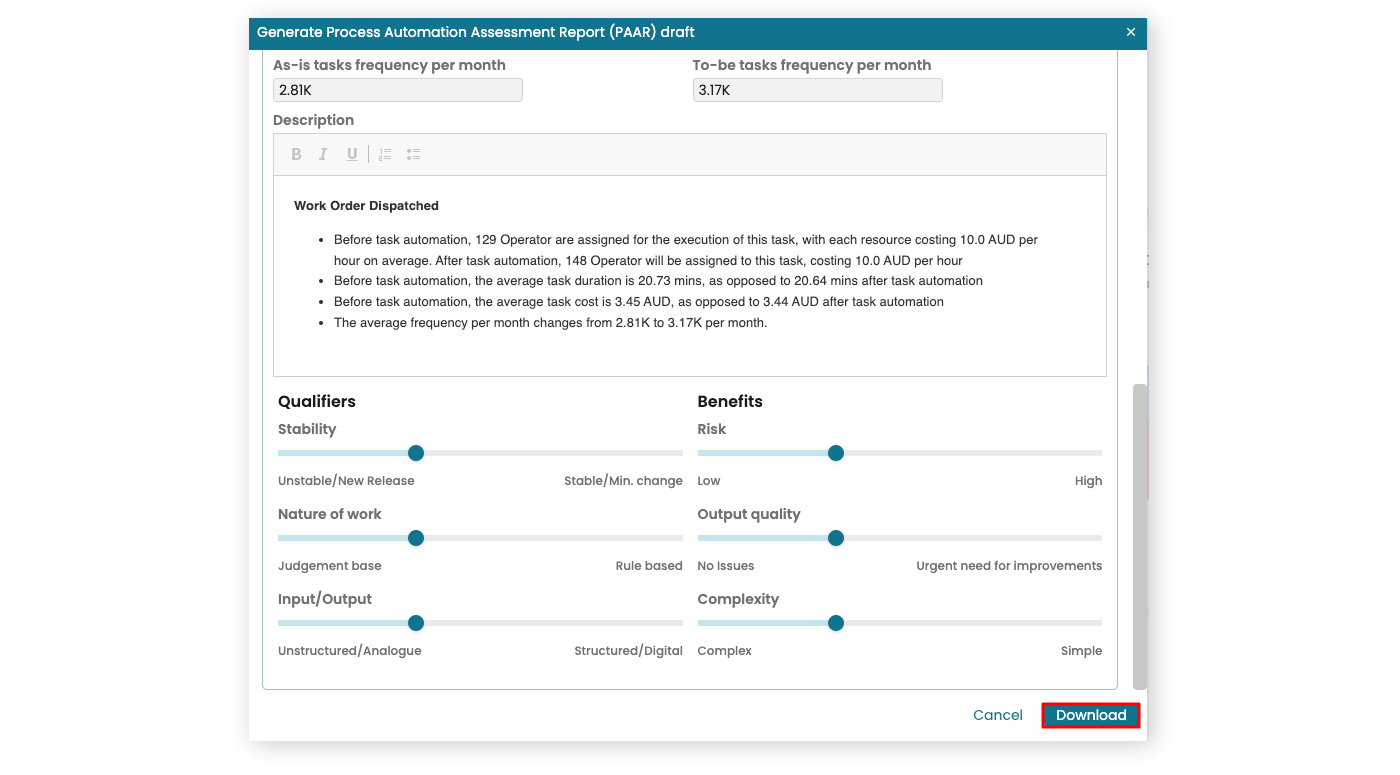
Start and Scale Intelligent Process Automation with Process Mining
To magnify efficiencies – and avoid magnifying inefficiencies that can cause intelligent automation efforts to fail – organizations must first gain visibility into existing operations and benchmark key performance indicators. Watch this on demand webinar to learn how to drive your intelligent process automation initiative with process mining.
Questions?
Ask an expert.
Get a personalized demo to see how Apromore can work for you.
Sign up for a free 30-day trial.
No strings attached.